Bethlehem Steel
- Tim Murphy
- Aug 18, 2019
- 8 min read
Updated: Apr 25, 2021
The rusting blast furnaces that tower over Bethlehem, Pennsylvania, once powered the largest shipbuilding company and second-largest steel manufacturer in the United States. For nearly 140 years, the Bethlehem Steel Corporation fueled American industry and development, revolutionizing the techniques and methods used to create high-grade iron and steel. It was Bethlehem Steel that supplied the materials necessary to win world wars and build modern cityscapes. The fires for each furnace have long been extinguished, but not forgotten by the citizens of Bethlehem. These decaying ruins of America's industrial might stand as a testament to the thousands of workers who toiled in its foundries and preserve the legacy of the "Arsenal of America."

The origins of Bethlehem Steel can be traced back to the Saucona Iron Company, founded by Augustus Wolfe in April 1857. The company supplied durable iron rails to Asa Packer and the Lehigh Valley Railroad—an important commercial transportation system that catalyzed the American Industrial Revolution and worked in conjunction with the Lehigh Canal to transport anthracite coal from rural mines to urban markets. However, before business operations could commence, the company’s development was hindered by the Panic of 1857, which caused drastic market price reductions for zinc, anthracite, and iron ore.
After the economy recovered in 1859, the company moved to South Bethlehem and changed its name to the Bethlehem Rolling Mill and Iron Company. In 1860, Bethlehem hired engineer John Fritz to construct its blast furnaces and rolling mills; however, due to the logistical complications of the Civil War, the structures weren’t completed until January 1863. In 1861, a group of investors led by Robert Sayre—chief engineer of the Lehigh Valley Railroad—assumed control of the foundry and formed the Bethlehem Iron Company. Alfred Hunt was named the company’s first president, a title he would retain until his death in 1888.
Bethlehem Iron showed modest success during its early years as it churned out rails for small market firms, but it could hardly compete with bigger foundries for more lucrative contracts. In response, the company turned its attention to steel manufacturing in the early 1870s. Before then, the United States relied heavily on foreign steel imports (from countries like Great Britain and Prussia) to meet consumer demands. Domestic mills constituted only a small fraction of total American steel supply. However, with the passage of the Schenck Tariff Act in 1871, hefty duties were levied on imported steel, which increased the demand for domestic production.
Bethlehem Steel was the first American steel mill to incorporate the revolutionary Bessemer process in its manufacturing methods. The process—discovered by Henry Bessemer in 1856—removes impurities from iron ore by blowing oxygen into molten pig iron. Coke and limestone are added to the mixture and help catalyze the oxidation process. The end result yields a product sixteen-times more durable than iron and substantially cheaper to manufacture. During Bethlehem’s first full year of operation utilizing the Bessemer process in 1875, the company manufactures roughly five percent of the nation’s steel rails. By 1879, it was producing over eleven percent.
Despite its modern industrial implements, Bethlehem still couldn’t rely on railroad accounts alone to make a profit, especially since it still faced stiff competition with corporations like Carnegie Steel. In the 1880s, the company secured a contract with the federal government to produce iron armor plates for the U.S. Navy as it upgraded and expanded its fleet. Eventually, Bethlehem was manufacturing armaments and ordinances for the entire U.S. military.
Between 1888 and 1892, the foundry constructed munitions depots, machine shops, and additional blast furnaces across its 1,000-acre campus to meet demand. Bethlehem’s immeasurable increases in manufacturing capacity and workforce earned it the distinction of being America’s first heavy-forging plant. Bethlehem displayed its awesome industrial power at the 1893 Chicago World’s Fair. The company supplied enough iron and steel to assemble the world’s first Ferris wheel, which stood 264 feet tall and held over 2,000 people.
In 1899, the company’s majority stockholders, Joseph Wharton and Robert Packer Linderman, decided to sell the rights to Bethlehem Iron and reorganize their business as the Bethlehem Steel Company. In 1901, Wharton put the company up for sale. He attempted to consolidate Bethlehem with British armaments group Vickers Sons and Maxim Limited and the Cramp Shipbuilding Group, but the deal fell through following lengthy negotiations. The majority of shares were instead acquired by Charles M. Schwab, president of the United States Steel Corporation.
Schwab began his career as an engineer and stake-driver at Andrew Carnegie’s steelworks in Braddock, Pennsylvania. His work ethic and productivity earned him frequent promotions. In 1887, Schwab was named general superintendent of the Homestead Works. A decade later, he became the president of the Carnegie Steel Company. In 1901, he sold Carnegie Steel to a group of investors led by J.P. Morgan and formed the U.S. Steel Corporation. When Schwab acquired Bethlehem Steel, he sold his shares to Morgan, thinking U.S. Steel would eventually absorb Bethlehem’s operations. However, in 1903, Schwab resigned from his position at U.S. Steel Corp., citing a poor working relationship with Morgan and other top executives. Schwab bought back his shares of Bethlehem Steel Company and formed the Bethlehem Steel Corporation in December 1904.

In 1907, Bethlehem Steel became the first manufactory to adopt Henry Grey’s innovative mill rolling process, which produced wide-flange ‘H’ beams (later patented as Bethlehem Beams) that were lighter, cheaper, and more structurally-sound than traditional ‘I’ beams. The corporation also replaced their Bessemer converters with open-hearth furnaces. These furnaces generated extremely high temperatures and allowed molten mixtures to be quality-tested repeatedly over a 24-hour period, which improved overall uniformity and integrity of the finished steel. Both of these advancements allowed skyscrapers to reach new heights and bridges to traverse greater distances.
Bethlehem Steel relied heavily on immigrant labor to meet production demands. Workers from various nationalities sought employment at the plant and transformed South Bethlehem into a vibrant, multicultural community virtually overnight. However, life was far from easy for these working families. Steelworkers often labored under treacherous conditions for grueling 14-hour shifts, 6-7 days per week. Accidents were unsettlingly common. Over 500 workers died on the job during the first half of the 20th century while thousands more were injured by molten metal, dangerous machinery, explosions, and toxic fumes.
Bethlehem’s exploitation of labor, meager pay, and anti-union policies prompted its workers to organize a strike on February 4, 1910. The strike was relatively uneventful as the plant maintained production with its willing labor force; however, on February 26, things turned violent when a parade of strikers marched on Bethlehem’s gates. The state police who were guarding the plant used excessive force to disperse the demonstrators, beating them back with batons and firing pistols into the air. One policeman fired a shot too low and wounded a striker in the leg. Another state trooper fired two shots into the lobby of the Majestic Hotel—a known meeting place for union organizers—killing one man, Joseph Szambo, and wounding another.
After 104 days of protest, the strike ended on May 18, 1910. Schwab and other Bethlehem executives agreed to grant workers optional overtime and Sunday work, but no wage increases. Although the steelworkers did not achieve all they had hoped, their strike drew national attention and prompted a federal investigation into Bethlehem’s company policies and working conditions.
Prior to World War I, Bethlehem Steel augmented its business interests to South America and Africa, acquiring higher-quality iron ore mines for cheaper prices compared to the domestic mines they had previously sourced from. The company entered the oceanic transportation and shipbuilding industries to exploit these global resources. Between 1905 and 1917, Bethlehem purchased numerous shipyards and manufacturing plants across the nation and consolidated their assets into the Bethlehem Shipbuilding Corporation, which would eventually become America’s largest shipbuilding enterprise.
During the early years of World War I, Bethlehem Steel served as a major armament and ammunition supplier to Allied governments, even though the United States implemented neutrality laws to prevent such transactions from happening. Schwab sidestepped these commercial regulations by distributing his goods to middlemen in Canada who would then transport Bethlehem’s products across the Atlantic.
Bethlehem’s business prospered all throughout the 1920s and even during the Great Depression. The company fabricated steel for some of America’s most famous structures, such as the Chrysler Building (c. 1930), Alcatraz Island (c. 1934), Hoover Dam (c. 1936), and the Golden Gate Bridge (c. 1937). By 1940, approximately eighty percent of the New York City skyline was constructed out of Bethlehem Steel.
After Charles Schwab’s death in September 1939, Bethlehem Steel’s primary ownership passed to Eugene Grace, the company’s acting president since 1916. When World War II broke out the same month of Schwab’s passing, Grace reportedly said, “Gentlemen, we are going to make a lot of money.” By the end of 1939, Bethlehem Steel received more than $1.3 billion in orders for ammunition, armor, and battleships.
High demand meant high production quotas and excessive overtime for Bethlehem’s employees. Steelworker representatives attempted to negotiate with Bethlehem executives for better pay and working conditions, but were unable to come to terms. The Steel Workers Organizing Committee (SWOC) intervened and called for a strike on March 24, 1941. Workers walked out across the company’s plants, freezing lucrative war-time production. When the company called in strikebreakers to disband the demonstrators, riots broke out across Bethlehem. For four days, the city was in turmoil. Pennsylvania Governor Arthur James declared a state of emergency and the protests gained national attention. Finally, on March 28, the SWOC and Bethlehem Steel agreed to raise worker wages, improve employee representation, and adhere to the policies of the National Labor Regulations Board. This landmark settlement paved the way for collective bargaining agreements and the ability to unionize under the United Steel Workers of America.
During World War II, Bethlehem’s workforce topped 31,000 employees, including several thousand women. The company was the largest single supplier of steel to the Allied Forces, producing 73 million tons of steel over the course of the war. Bethlehem manufactured nearly one-third of the armor plating and heavy guns used by the United States and constructed an average of one battleship per day in 1943.
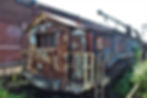
With the devastation of war came Bethlehem’s most productive years, fueled by a dependent global economy and derelict European infrastructure. During the 1950s, Bethlehem manufactured an average of 23 million tons of steel per year, most of which was exported to rebuilding nations. In addition, the company secured contracts with the federal government to supply materials for the nation’s evolving nuclear and aerospace industries.
However, Bethlehem’s post-war prosperity did not last long. When Japan and Germany reconstructed their steel plants during the mid-20th century, they implemented innovative manufacturing technologies, such as basic-oxygen furnaces and continuous casting, which made high-quality steel at drastically lower prices compared to Bethlehem’s open-hearth methods. The company also faced growing competition with the plastic and aluminum industries and “mini-mills”—small electric furnaces that melted scrap metal into simple iron and steel products at a lower cost than most steel corporations.
Bethlehem’s top executives hesitated to upgrade their facilities out of concern for their bottom dollar. Consequently, construction projects and building firms increasingly rejected Bethlehem’s bids for steel supply as foreign imported steel was substantially cheaper. In the early 1980s, a global recession rocked America’s outdated and underperforming industrial plants. Bethlehem Steel reported a loss of $1.5 billion in 1982 which initiated a domino effect that shut down many of its operations. On November 18, 1995, Bethlehem’s main plant rolled out steel for the last time. All operations in Bethlehem ended by 1998. The company declared bankruptcy in 2001 and dissolved in 2003, effectively ending the region’s industrial age.
Today, the main steel plant has been revitalized and preserved, the center of Bethlehem’s vivacious arts and entertainment district known as SteelStacks. Visitors can tour the nearby National Museum of Industrial History, experience a concert at the Levitt Pavilion, or observe Bethlehem’s blast furnaces along the Hoover-Mason Trestle. The trestle originally supported a narrow-gauge electric trolley that transported raw materials from the ore yards to the blast furnaces. Now it is a pedestrian walkway that displays informative plaques about Bethlehem Steel’s industrial and cultural histories. Bethlehem Steel is an exceptionally fascinating destination that epitomizes the rise, fall, and revival of American industry. It is incredibly comforting to witness a community rally around such a historic landmark and advocate for its continued protection, preservation, and appreciation.
For more information on Bethlehem Steel's history, visit Explore PA History and Penn State's Online Library!
Check out SteelStacks for more info on upcoming concerts and events!
Visit Abandoned America for an insider look at the plant and check out Opacity for some old photos from Bethlehem Steel's active years!
For an economic history of Bethlehem Steel, visit Funding Universe!
Watch The People Who Built America on YouTube to hear interviews with some of Bethlehem's steelworkers!
Learn more about the Steel Strike of 1910 by watching and reading this History Headline!
Read this resource on Google Books: Warren, Kenneth. Bethlehem Steel: Builder and Arsenal of America. University of Pittsburgh Press. 2008.